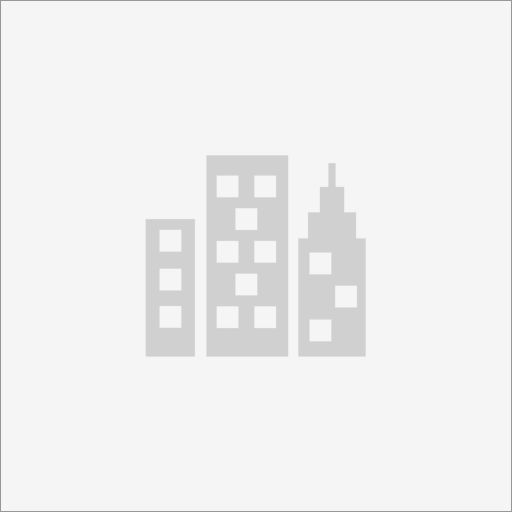
Argotec
SPACE FOR AMBITIONS
Operations in Argotec is a revolution in the aerospace small satellites business, with a focus on accuracy and exceptional service. Our target is to produce and delivery satellites as a technological factory. Maintenance as a part of Industrialization & Processes department, it is the business partner that work tirelessly behind the scenes to make it all happen. We drive continuous improvement and maintain all equipment to ensure our customers are satisfied by an incredible and reliable product.
We are primarily interested in a demonstrated commitment to the work and the potential to grow. Experience comes in many forms and passion goes a long way. If your experience is close to what we’re looking for, please consider applying.
Your expertise is needed to improve our cutting-edge technology. Our team works in a collaborative and Agile environment and our products range from, advanced CubeSats, advanced electronic systems and mission payloads.
A PDM plays a crucial role in managing and organizing product-related information within Argotec. Here are some key aspects of this role:
- Data Management: The PDM is responsible for collecting, organizing, and maintaining data related to products. This includes information about materials, design schematics, bills of materials, and manufacturing processes.
- Bridge Between Technical and Production Teams: PDM facilitates communication between the engineering (which creates design drawings) and operation (which manages production and logistics). The PDM ensures that both departments have access to accurate and up-to-date information.
- Change Management: When changes are made to products (such as design corrections or material updates), the PDM ensures that these changes are documented and communicated to all relevant stakeholders.
- Integration with CAD Systems: Given the widespread use of Computer-Aided Design (CAD) systems in product design, the PDM must be proficient in integrating these tools with the data management system.
- Configuration Management: The PDM establishes standard procedures for data management and ensures that different versions of drawings and specifications are tracked and controlled.
- Product Lifecycle Management: Responsible for managing the entire lifecycle of products, from idea generation, through design and development, to production, to operations.
In this role, you will be able to
- Act as mediator between Production, Engineering and Procurement stakeholders
- Ensure proper communication and information sharing among the operators supporting internal manufacturing and assembly activities
- Supervise digitalization activities across all active projects, including initial product digitalization, change management, and deployment of new releases
- Oversee design, implementation, and maintenance of data pipelines, and data processing systems
- Develop strategic plans and ensures tactical execution of these plans
- Responsible for maintaining best practices and data model standards
- Assist supply chain management wrt special projects (e.g., including on-off, prototypes etc.)
- Support development of proposals regarding new products and services
- Support definition and commission of assembly and test plans and cycles
- Assist the definition and periodic review of internal coding standards used for item tracking at all levels
- Assist with long-lead items management and part obsolescence for existing products
- Assist Program Managers during the execution of complex projects
DUTIES
- Develop and implement Configuration Management Plans and drive data quality across products and projects
- Develop and implement integrated Product Lifecycle Management (PLM) plans and procedures
- Develop and implement documentation management processes that allow for efficient data storage, search, and retrieval
- Assist in implementing hardware and software version control processes, policies and procedures
- Assist in the use of configuration management tools to store, track, and manage configuration items
- Manage data archiving
- Manage document searches using the document metadata. In the specific case of the technical drawing are usually identified with the data entered in the entry table also called cartouche;
- Manage storage of technical specifications automatically within a database that regulates the business cycle
- Allows viewing of archived documents in lightweight formats (in PDF or, for CAD formats, in DWF, Adobe and Autodesk formats respectively).
REQUIRED EXPERIENCES & SKILLS
- High School Diploma
- Previous experience in the area of product and data configuration management (at least one year)
- Good knowledge of the mains ERP on the market (SAP B1)
- Demonstrated experience with Atlassian tools, including Jira and Confluence
- Demonstrated experience with source control tools, such as Git or Subversion
- Knowledge of MES systems
- Knowledge of fully integrated PLM tools and methodologies is a plus
Argotec is an equal-opportunity Employer. This announcement is aimed at both sexes, under laws 903/77 and 125/91, and to people of all ages and all nationalities, under legislative decrees 215/03 and 216/03.
To apply for this job please visit invia-candidatura.